Infusion, vacuum bagging, hand lay up, bla, bla, bla. It's all marketing-speak until the hull hits the water.
There's been plenty written lately about the new techniques employed in making fiberglass boat parts. To most consumers it's simply not that important. Performance, interior features and accommodations top the list of priorities for many. But, with the large monetary investments that we have in our boats, shouldn't we know that the integrity of the entire vessel is tied to the quality of the construction of the major fiberglass parts? The straight answer is yes and the best technique currently being employed to do this work is Back Cove's VIP Resin Infusion Technology.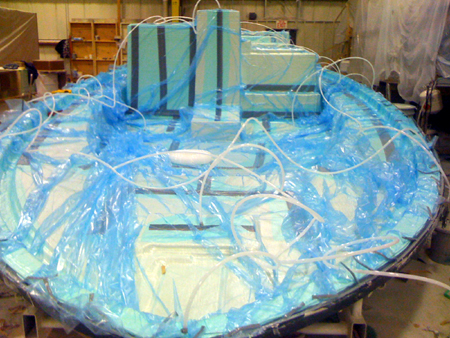
The basics of the system follow herein but you are always welcome to come to either the Back Cove or Sabre facilities to witness this process for yourself. In the good old days we rolled out pieces of dry fiberglass woven roving and liberally applied resin to the cloth in order to create the stack of materials which became the fiberglass part. We then squeezed out the resin and air as best we could using rollers and brushes. Glass to resin ratios in these hand laid parts was typically in the 40/60 range.
Today's technique involves applying the gelcoat (exterior color) to the mold. Then all materials including the coring are applied dry, using an adhesive to temporarily hold the layers together. Then we insert supply lines and pull and large one.jpgece plastic cover over the entire part, sealing the edges against the mold so that air cannot escape. Once the part is ready we start the flow of resin which is drawn into the bag as pressure is applied to remove all of the air. Within an hour the resin flows from it's entry points to the dry fiberglass, wetting it out and removing air voids. Typical glass to resin ratios in this type of part are in the 60/40 range.
The process is far cleaner and emits fewer VOC's (Volatile Organic Compounds) into the environment so everyone benefits, not just the boat buyer. The parts are lighter and they are stronger because they have a better glass to resin ratio. Lighter powerboats burn less fuel too so the gains are ongoing.
When considering a new fiberglass boat or even if you are considering new versus used boats, think about the integrity of a resin infused part. It truly is better for you and for the environment that we live in.
Look for an upcoming article about Back Cove's VIP process written by boating expert Eric Sorensen who recently spent a day in our glass shop. He was most impressed with the process we employ.